Comment réduire les pertes de produits avec une pulvérisation plus précise
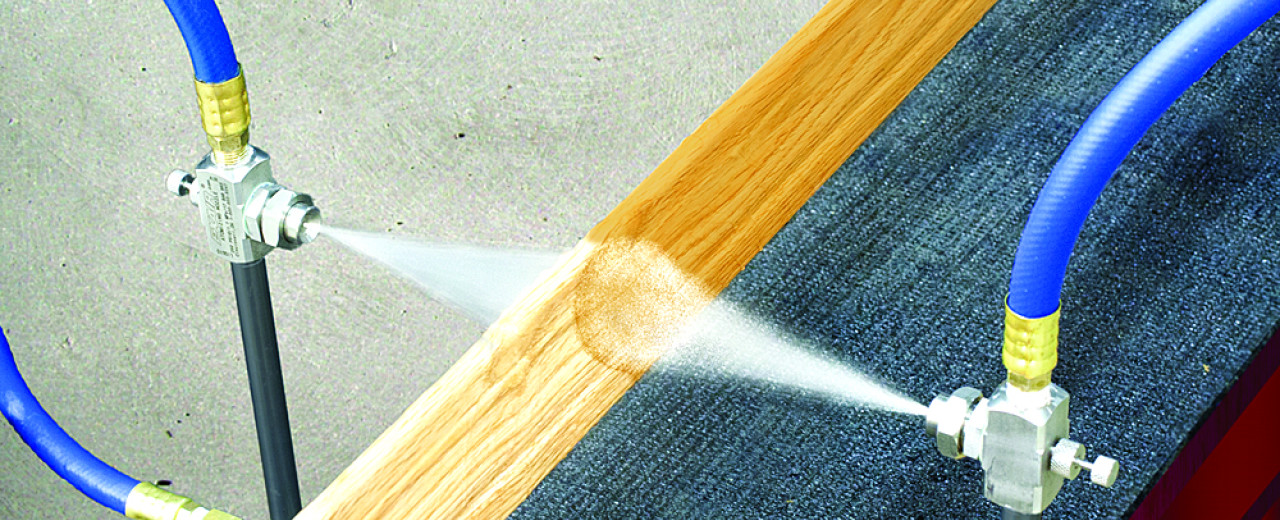
Dans un contexte industriel où chaque goutte compte, l'optimisation des systèmes de pulvérisation représente un levier de performance souvent sous-estimé. Que vous utilisiez des liquides coûteux, des produits chimiques sensibles ou de simples solutions aqueuses, les pertes générées par une pulvérisation inefficace peuvent représenter jusqu'à 30% de votre consommation totale. Ces pertes impactent non seulement votre budget opérationnel, mais également l'empreinte environnementale de votre activité et la qualité de vos produits finis. La bonne nouvelle ? Des solutions existent pour transformer radicalement l'efficacité de vos applications par pulvérisation, et elles commencent par la compréhension et la sélection appropriée de vos buses d'atomisation.
L'impact économique et environnemental des pertes de produit
La quantification des pertes de produit révèle souvent des chiffres alarmants qui pèsent lourdement sur la rentabilité des opérations industrielles.
Le coût caché des inefficacités de pulvérisation
Les pertes de produit ne se limitent pas au simple gaspillage de matière première. Elles engendrent une cascade de coûts supplémentaires :
-
Surconsommation des produits pulvérisés (jusqu'à 30% de gaspillage)
-
Augmentation des besoins en traitement des effluents et déchets
-
Coûts de nettoyage des surfaces non ciblées
-
Temps de production perdu lors des réapplications nécessaires
-
Défauts de qualité entraînant des rebuts et des reprises
Une étude menée dans le secteur de l'industrie alimentaire a démontré qu'une optimisation des systèmes de pulvérisation peut réduire la consommation de produits de nettoyage de 15 à 20%, ce qui représente une économie annuelle moyenne de 24 000 € pour une ligne de production standard.
L'enjeu environnemental
Au-delà de l'aspect financier, les pertes de produit générées par une pulvérisation imprécise présentent des défis environnementaux significatifs :
-
Augmentation de la charge polluante des eaux usées
-
Émissions accrues de composés organiques volatils (COV)
-
Contamination potentielle des espaces de travail
-
Plus grande empreinte carbone liée à la production et au transport des produits gaspillés
L'optimisation de vos systèmes de pulvérisation s'inscrit donc parfaitement dans une démarche de développement durable et de responsabilité environnementale.
Les fondamentaux d'une pulvérisation efficace
La maîtrise des principes de base qui régissent la pulvérisation est essentielle pour comprendre comment réduire les pertes et améliorer la précision de vos applications.
Le triangle d'or de la pulvérisation
Une pulvérisation efficace repose sur trois paramètres interdépendants formant ce que les experts appellent le "triangle d'or" :
-
La pression : détermine la portée, la taille des gouttelettes et le débit
-
Le débit : quantité de liquide pulvérisée par unité de temps
-
L'angle de pulvérisation : définit la zone de couverture et la distribution du produit
La modification d'un seul de ces paramètres affecte automatiquement les deux autres. Par exemple, augmenter la pression augmentera le débit et modifiera la taille des gouttelettes, produisant généralement des particules plus fines susceptibles de dériver hors de la zone cible.
La physique des gouttelettes : taille et distribution
La taille des gouttelettes joue un rôle crucial dans l'efficacité de la pulvérisation :
-
Les gouttelettes trop fines (< 50 microns) sont sujettes à l'évaporation rapide et à la dérive
-
Les gouttelettes trop grosses (> 300 microns) peuvent rebondir sur les surfaces et créer un ruissellement
-
La distribution optimale dépend de l'application spécifique et de la surface cible
Une buse d'atomisation bien choisie produira un spectre de gouttelettes adapté à votre application particulière, minimisant ainsi les pertes par dérive ou ruissellement.
Sélectionner la buse d'atomisation optimale pour votre application
Le choix de la buse d'atomisation représente la décision la plus importante pour améliorer l'efficacité de votre système de pulvérisation et réduire les pertes de produit.
Les buses à jet plat : précision et uniformité
Les buses à jet plat produisent un motif d'atomisation elliptique particulièrement adapté aux surfaces planes ou aux applications nécessitant un chevauchement uniforme.
Caractéristiques et avantages :
-
Distribution uniforme du liquide sur toute la largeur du jet
-
Excellent contrôle de la couverture grâce à des angles précis (entre 15° et 110°)
-
Réduction des pertes grâce à une application ciblée
-
Options disponibles pour les applications à faible et haute pression
Applications idéales :
-
Application de revêtements sur des surfaces planes
-
Nettoyage de tapis roulants
-
Pulvérisation de lubrifiants
-
Rinçage de pièces
-
Systèmes de pulvérisation en rideau nécessitant un chevauchement uniforme
Les buses à jet plat de dernière génération intègrent souvent des technologies anti-dérive qui réduisent considérablement les pertes tout en maintenant une couverture optimale. Ces buses produisent des gouttelettes plus grosses et plus consistantes, moins susceptibles d'être emportées hors de la zone cible.
Les buses coniques : couverture et pénétration
Les buses coniques se divisent en deux catégories principales : les buses à cône plein et les buses à cône creux, chacune offrant des avantages spécifiques pour réduire les pertes de produit.
Buses à cône plein :
-
Distribution uniforme du produit dans tout le volume du cône
-
Excellente résistance au colmatage grâce aux passages plus larges
-
Gouttelettes de taille moyenne à grande réduisant les risques de dérive
-
Couverture complète idéale pour les applications volumétriques
Ces buses sont particulièrement efficaces pour les applications de refroidissement, l'extinction d'incendies, l'humidification où une couverture complète est essentielle pour éviter les zones sèches génératrices de défauts.
Buses à cône creux :
-
Concentration du liquide sur la périphérie du cône
-
Production de gouttelettes plus fines pour une meilleure atomisation
-
Excellente pénétration dans les zones difficiles d'accès
-
Réduction de la consommation de liquide grâce à une atomisation efficace
Les buses à cône creux excellent dans les applications nécessitant une bonne atomisation du produit, comme la pulvérisation de pesticides, le refroidissement de gaz ou le lavage de fumées. Leur conception permet de maximiser la surface de contact entre le liquide et l'air ou la surface traitée.
Les buses spécialisées : la solution aux problèmes spécifiques
Pour les applications particulièrement exigeantes, des buses spécialisées peuvent offrir des solutions sur mesure pour minimiser les pertes :
Buses à chambre de pré-atomisation :
Ces buses incorporent une chambre qui prépare le liquide avant son éjection, produisant des gouttelettes de taille plus homogène et réduisant significativement la production de fines particules sujettes à la dérive.
Buses à induction d'air :
En incorporant de minuscules bulles d'air dans les gouttelettes, ces buses produisent des particules plus grosses mais plus légères, qui éclatent en multiples microgouttelettes au contact de la cible. Cette technologie permet de réduire les pertes par dérive de 50 à 80% par rapport aux buses conventionnelles.
Buses à réduction de débit (LDR) :
Conçues pour maintenir une pression constante malgré les variations de débit, ces buses permettent d'ajuster précisément la quantité de produit appliquée sans modifier le motif de pulvérisation, évitant ainsi le surdosage.
Technologies avancées pour une pulvérisation de précision
L'évolution technologique a permis le développement de systèmes sophistiqués qui transforment radicalement l'efficacité des opérations de pulvérisation.
Systèmes de pulvérisation contrôlés par ordinateur
Les systèmes automatisés de contrôle de pulvérisation représentent une avancée majeure dans la réduction des pertes :
-
Ajustement dynamique de la pression en fonction des conditions changeantes
-
Contrôle précis du débit pour maintenir un dosage constant
-
Surveillance en temps réel de la performance de pulvérisation
-
Arrêt automatique en cas de détection d'anomalies
Ces systèmes permettent d'économiser jusqu'à 25% de produit par rapport aux méthodes manuelles traditionnelles, tout en assurant une application plus uniforme.
Capteurs et technologies de détection
L'intégration de capteurs sophistiqués offre de nouvelles possibilités pour optimiser la pulvérisation :
-
Capteurs de présence activant la pulvérisation uniquement lorsque le produit est détecté
-
Systèmes de vision artificielle identifiant la forme et la position exactes de la cible
-
Capteurs d'uniformité évaluant la couverture en temps réel
-
Moniteurs de débit alertant en cas de dysfonctionnement
Un fabricant de composants électroniques a réduit sa consommation de solvant de nettoyage de 32% en installant des capteurs de présence qui activent les buses uniquement lorsque des circuits imprimés sont détectés sur la ligne.
Optimisation des paramètres de pulvérisation
Au-delà du choix de la buse, l'ajustement précis des paramètres opérationnels constitue un levier puissant pour réduire les pertes de produit.
Pression et débit : trouver l'équilibre parfait
La relation entre pression et débit est fondamentale pour une pulvérisation efficace :
-
Une pression trop faible peut produire des gouttelettes trop grosses et une couverture irrégulière
-
Une pression excessive génère des gouttelettes fines sujettes à la dérive et augmente l'usure des buses
-
Le débit optimal dépend de la vitesse de déplacement de la cible et de la quantité de produit requise
Pour la plupart des applications industrielles, opérer dans la zone médiane de la plage de pression recommandée pour votre buse offre le meilleur compromis entre efficacité et contrôle.
Formule pratique :
Pour calculer le débit requis (Q) en fonction de la dose souhaitée (D), de la vitesse d'avancement (V) et de la largeur de travail (L) :
Q (L/min) = D (L/ha) × V (km/h) × L (m) / 600
Distance et angle de pulvérisation
La position de la buse par rapport à la cible influence directement l'efficacité de l'application :
-
Une distance trop faible concentre le produit sur une zone restreinte et peut endommager la surface
-
Une distance excessive augmente les pertes par dérive et réduit la force d'impact
-
L'angle optimal dépend de la géométrie de la cible et du type d'application
Un positionnement correct de la buse peut réduire les pertes de produit de 10 à 15% simplement en assurant que le motif de pulvérisation couvre précisément la zone cible sans débordement.
Viscosité et température du produit
Les propriétés physiques du liquide pulvérisé affectent significativement la qualité de l'atomisation :
-
Une viscosité trop élevée peut générer une atomisation grossière et irrégulière
-
Une température inadaptée peut modifier la viscosité et donc le comportement du produit
-
Certains produits requièrent des ajustements spécifiques de température pour une atomisation optimale
Pour les produits visqueux, l'utilisation d'un système de chauffage ou le choix de buses spécifiquement conçues pour les liquides à haute viscosité peut améliorer considérablement l'efficacité de la pulvérisation et réduire les pertes.
Maintenance préventive : garantir la performance à long terme
Un programme de maintenance rigoureux est essentiel pour maintenir l'efficacité de votre système de pulvérisation et prévenir les pertes de produit liées à l'usure ou aux dysfonctionnements.
Inspection et nettoyage réguliers
La routine d'entretien la plus basique mais essentielle comprend :
-
Inspection visuelle quotidienne des buses pour détecter les obstructions ou dommages
-
Nettoyage hebdomadaire avec des solutions adaptées aux matériaux des buses
-
Vérification mensuelle des motifs de pulvérisation pour identifier les signes d'usure
-
Rinçage complet du système après utilisation de produits susceptibles de sécher ou cristalliser
Un simple nettoyage régulier peut prolonger la durée de vie des buses de 30 à 50% et maintenir une performance optimale.
Quand et comment remplacer les buses usées
L'usure des buses est inévitable mais gérable :
-
Remplacez les buses lorsque leur débit dépasse de 10% les spécifications d'origine
-
Changez toutes les buses simultanément pour maintenir l'uniformité de l'application
-
Conservez un stock de buses de rechange pour minimiser les temps d'arrêt
-
Documentez les remplacements pour identifier les zones d'usure prématurée
Une étude dans l'industrie agroalimentaire a démontré qu'une buse dont le débit avait augmenté de seulement 15% en raison de l'usure pouvait entraîner un surcoût annuel de 5 000 € en produits gaspillés.
Filtration et qualité du liquide
La contamination du liquide est une cause majeure de dysfonctionnement des buses :
-
Installez des filtres adaptés à la taille de l'orifice de vos buses
-
Nettoyez ou remplacez régulièrement les éléments filtrants
-
Utilisez si nécessaire des systèmes de traitement d'eau pour éliminer les minéraux causant l'entartrage
-
Surveillez la qualité du liquide, particulièrement sa dureté et sa teneur en particules
Un système de filtration correctement dimensionné peut réduire le taux de remplacement des buses de 40% tout en assurant une performance constante.
Transformer les pertes en profits
L'optimisation des systèmes de pulvérisation représente une opportunité souvent négligée d'améliorer significativement la rentabilité et la durabilité des opérations industrielles. En choisissant judicieusement vos buses d'atomisation, en optimisant les paramètres opérationnels et en mettant en place un programme de maintenance rigoureux, vous pouvez transformer les pertes de produit en gains substantiels.
Ne laissez pas votre produit – et vos profits – s'évaporer dans l'air. Prenez dès maintenant les mesures nécessaires pour transformer votre système de pulvérisation en un atout stratégique pour votre entreprise.
Vous souhaitez aller plus loin dans votre démarche d’optimisation ?
Découvrez notre gamme de buses d'atomisation sur notre site web Kermaz Pneumatic.
Contactez nos experts pour des conseils avisés et un accompagnement personnalisé :
✉️ contact@kermaz-pneumatic.com
☎️ 01 69 30 69 80
Optimisez vos procédés industriels dès maintenant grâce à une gestion intelligente de l’air comprimé !